Clean Room: Why It’s Crucial for High-Quality PPF Installations
When it comes to installing paint protection film (PPF) on your vehicle, you might think that getting the right film and a skilled installer is all that's necessary. However, it's important to note that the cleanliness of the installation space is crucial. A clean room isn’t just a nice-to-have; it's essential for ensuring your PPF looks great and lasts as long as possible. Maintaining a tidy environment not only minimizes dust but also enhances the adhesive bond.
A clean room is crucial for paint protection film installations because it minimizes the presence of dust and debris, which can cause imperfections such as peeling and bubbling in the film. By maintaining a controlled environment, installers can enhance the adhesion and overall durability of the PPF, leading to better performance and longer-lasting results.
Why Room Cleanliness is Essential for PPF Installation
A clean room is crucial because it creates the ideal conditions for applying PPF without the interruption of contaminants. Dust, dirt, and even airborne particles can significantly disrupt your installation process, resulting in unsightly bubbles and imperfections that negatively impact both performance and appearance. Imagine spending hours preparing your vehicle only to uncover tiny blemishes once the film is applied. It’s disheartening and could result in rework, wasted resources, or worse, a dissatisfied customer.
- Enhanced Visual Quality: For many enthusiasts, having a perfect finish isn't merely about protection; it's about pride. Whether you’re wrapping a cherished classic car or a modern luxury vehicle, visual quality is paramount. A clean room minimizes the risks associated with dust particles during installation, allowing for an immaculate application. This ensures that when customers step back to admire their newly protected vehicle, they're greeted with smooth surfaces devoid of bubbles or creases caused by unwanted debris. Clean rooms are characterized by stringent environmental controls that create the perfect zone for such delicate work. With particle counts at less than 1,000 particles per cubic meter, the difference is clear: high-quality results versus visual defects that tarnish the hard work put into enhancing or preserving a vehicle's aesthetic allure.
- Extended Durability: However, cleanliness in the installation environment isn’t solely about looks. It plays a vital role in ensuring durability as well. Contaminants like dust and grease can significantly diminish the life of your PPF by impacting how effectively it adheres to the surface. An optimal adhesive bond is essential; otherwise, early wear and tear can lead to peeling or lifting of the film prematurely. This aspect not only frustrates installers but can leave end-users disappointed if they expect longevity from their investment.
By maintaining clean room standards during the installation process, manufacturers can significantly extend the lifespan of PPF applications—providing value-added service while meeting regulatory compliance and enhancing brand reputation.
Common Contaminants in PPF Installations
Contaminants are any unwanted substances that can interfere with the PPF adhesive process. They play a critical role in determining the quality and longevity of the film once applied. Among the most common culprits are dust, oils, grease, and environmental particulates. Each presents unique challenges during installation.
- Dust and Debris: Dust is the most ubiquitous contaminant found in environments where PPF installations take place. This tiny foe is often overlooked; however, it can settle on both the film and the car surface during application. When this occurs, unsightly bubbles may form or, worse, weak adhesion, which ultimately compromises the effectiveness of the protection film. The sizes of dust particles range between 0.5 and 10 micrometers, demonstrating how small they can be yet still cause significant issues. A meticulous cleaning strategy that includes regularly wiping down surfaces can serve as your first line of defense against these intrusive particles.
- Oils and Grease: Another crucial concern is oils and grease, which can arrive from various sources, including fingerprints left by technicians or residues from equipment. Even a seemingly small amount of grease can significantly compromise the adhesive bonding strength required for durable installations. Just 0.1 to 0.5 mg/cm² of contamination can severely hinder performance. To mitigate this risk, it's recommended for installers to wear gloves and use specialized cleansers specifically designed to remove oils without leaving behind any residue. This ensures a clean surface ready for optimal adhesion.
- Environmental Particulates: Furthermore, we cannot dismiss environmental particulates such as pollen and airborne bacteria, which also pose a threat to adhesion quality. These microscopic invaders can infiltrate the workspace without notice, leading to defects like peeling or bubbling after installation. To combat this issue, many clean rooms employ HEPA filters that capture such contaminants, creating a substantially safer environment for both technicians and customers alike.
Professional Techniques for a Clean Workspace
Professionals know that every detail matters when it comes to installing paint protection film, which is why they implement stringent techniques to keep their workspaces spotless. One of the first steps involves establishing regular cleaning cycles. This isn't just about tidying up occasionally; it's a systematic approach where installers commit to daily vacuuming and weekly deep cleaning of the installation area. By doing so, they prevent even the smallest dust particles from accumulating on surfaces. Think of an artist preparing their canvas—any little speck can ruin a masterpiece, and the same applies here.
Regular cleaning also requires attention to detail in maintaining tools and equipment used during installations. Professionals often have dedicated storage for their supplies, ensuring everything remains organized and clean. Just as one would not want to paint with dirty brushes, using contaminated tools could lead to suboptimal PPF application results. Specialized equipment plays a critical role in ensuring a contaminant-free environment. For instance, air filtration systems are essential tools within professional studios. Technicians often use HEPA-filtered vacuums and air purifiers that trap airborne particles before they settle on working surfaces or the vehicle itself. It’s like having a silent guardian against dust! Furthermore, anti-static mats are becoming increasingly popular among professionals; these mats attract dust particles, preventing them from becoming airborne and settling on cars while the film is being applied.
Enhancing Adhesion and Clarity with a Clean Room
In the world of PPF applications, ensuring a controlled environment plays a significant role, especially when it comes to adhesion. Clean environments boost the adhesive capabilities of PPF in remarkable ways. When PPF is applied in clean rooms, it maintains 95% of its initial adhesion strength after six months, while those applied in less controlled conditions drop down to merely 80%. This improvement is crucial because an optimal bond means longer-lasting protection for vehicles and surfaces alike. When you consider this difference, it's clear that investing time in maintaining a clean workspace is not only about immediate results but also profound longevity in a product's performance.
- Increased Adhesion: But what does this increased adhesion mean for the end user? Think of it this way: a vehicle’s exterior is constantly bombarded by elements—from road grime to UV rays. When PPF sticks firmly and reliably due to a clean installation environment, it acts as an effective barrier. This prevents scratches and preserves the paint job underneath. Thus, when looking at your vehicle, you’re not just admiring its aesthetics but also appreciating the smart investment you made in protecting its value.
- Superior Clarity: By ensuring such meticulous cleanliness during installation, small particles are kept at bay. This helps maintain the film’s seamless integration with the vehicle's surface, which enhances both clarity and glossiness. Vehicles treated with properly installed PPF exhibit enhanced shine—making them look showroom-ready for years to come. Installations conducted in clean rooms have substantially lower incidences of delamination compared to those in uncontrolled environments—by as much as 30%!
If you're investing in PPF for your vehicle, achieving superior clarity through clean room technology isn't just about looks; it fortifies performance too.
Cost and Efficiency Benefits of a Clean Room
Maintaining a clean room is an investment that quickly pays off. One of the most significant benefits is reduced rework; when installations are conducted in a contaminant-free environment, the rate of rework drops by over 40%. This means fewer returns and adjustments due to dust or particles trapped under the film. Lowering your rework rate directly results in decreased labor costs since technicians can focus on new installations rather than correcting mistakes, making every minute in the clean room count.
Faster Installation
Another noteworthy benefit lies in significantly faster installation times. When technicians work in an environment free from allergens and particles, they can move through their tasks without interruption. In fact, studies show that installation times can decrease by 10-15%, primarily because technicians aren’t constantly stopping to wipe down surfaces or clear out debris. Think about it—when you’re not continually pausing to manage contaminants, your workflow becomes streamlined; it's akin to racing on a perfectly maintained track versus navigating through rocky terrain.
Long-term Savings
While the initial expenditure on cleanroom technology and ongoing maintenance might seem daunting, consider the long-term savings. The financial implications of reduced waste are profound: with a well-maintained clean room, installers minimize the amount of film lost during flawed applications, which can lead to an impressive reduction in costs over time. Moreover, cleaner installations lead to higher customer satisfaction rates since clients appreciate flawless finishes. This elevates your business's reputation and encourages repeat customers who trust your expertise—all translating into increased revenue.
Top Tips for Achieving Optimal PPF Results
To achieve exceptional results from your paint protection film (PPF) installation, meticulous attention to both your environment and technique is paramount. One of the most significant factors is ensuring you're using high-quality products.
- Use Quality Products: Selecting premium PPF brands is not just a matter of preference; it can drastically influence the effectiveness and longevity of the film. High-quality films possess enhanced adhesion properties, making them less susceptible to lifting or peeling over time, and they offer superior clarity that maintains your vehicle's original appearance. Imagine investing in a protective layer that looks as good on day one as it does after months on the road—this assurance is only found with top-tier brands. Avoiding lower-tier options saves you from future headaches caused by contamination or environmental wear.
- Keep Your Workspace Organized: A well-structured workspace can make all the difference during the PPF installation process. Consider establishing designated zones for each phase: preparation, installation, and post-application checks. Keeping these areas separate streamlines your workflow and minimizes cross-contamination risks. When every tool has its place and no clutter surrounds you, it's easier to focus entirely on the task at hand without distractions. Furthermore, an orderly environment contributes to maintaining cleanliness, which directly impacts the final result.
- Regular Training: Continuous training for technicians is essential—not just on installation techniques but also on cleanliness protocols. When everyone adheres to a consistent standard regarding maintaining a clean environment, it results in higher-quality installations overall. Think of it like a choir; when each member knows their part inside out and can harmonize with others, the outcome is far greater than any single voice alone could achieve. Investing in regular workshops helps ensure everyone involved understands best practices and stays up-to-date with industry innovations.
- Final Inspection: Never underestimate the importance of conducting a final inspection under bright lighting. This step serves as your opportunity to catch any imperfections or contaminants that might have slipped through unnoticed during application. Just like an artist signs their name after a masterpiece, this inspection confirms that every detail aligns with your high standards. Look closely for bubbles or debris trapped beneath the film; these issues can mar what would otherwise be a flawless result.
By incorporating these best practices into your routine, you enhance the quality of your PPF installations and ensure longevity and durability that truly protect your investment. In summary, achieving high-quality PPF installations requires more than just skill; it necessitates dedication to cleanliness and organized processes at every stage of installation.
Superior PPF Services in Melbourne, FL
Your vehicle deserves more than just a wash—it deserves protection that lasts. At JL’s Showroom Auto Salon in Melbourne, FL, our
expert paint protection film (PPF) installation
helps shield your car from chips, scratches, and Florida’s harsh sun. With precision application and top-tier film materials, we ensure your ride maintains a sleek, showroom-quality finish even after years on the road. Trust our team to help preserve the beauty and value of your investment with durable, invisible protection.
Schedule your PPF appointment today
and give your car the defense it needs against daily wear and tear!
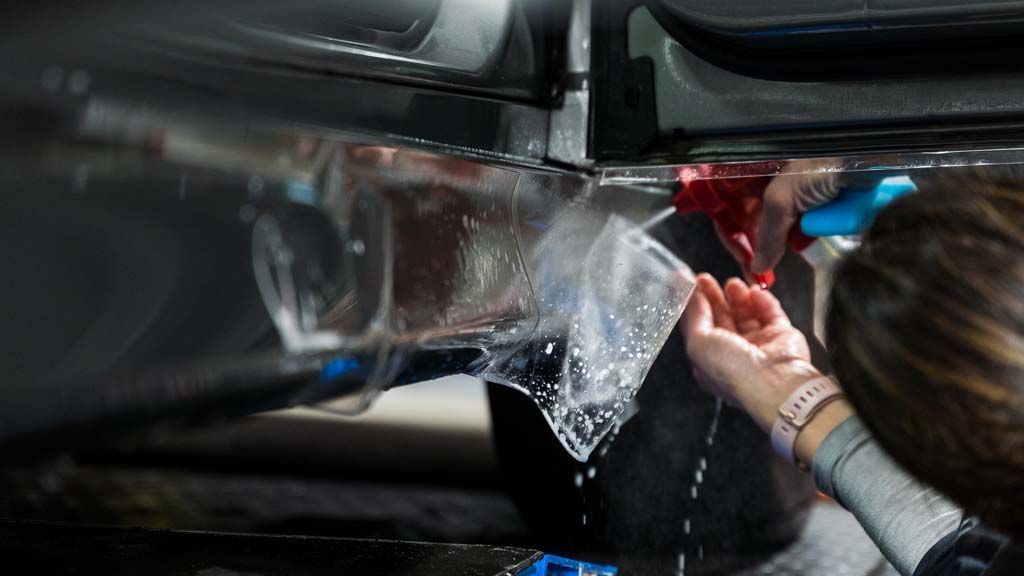
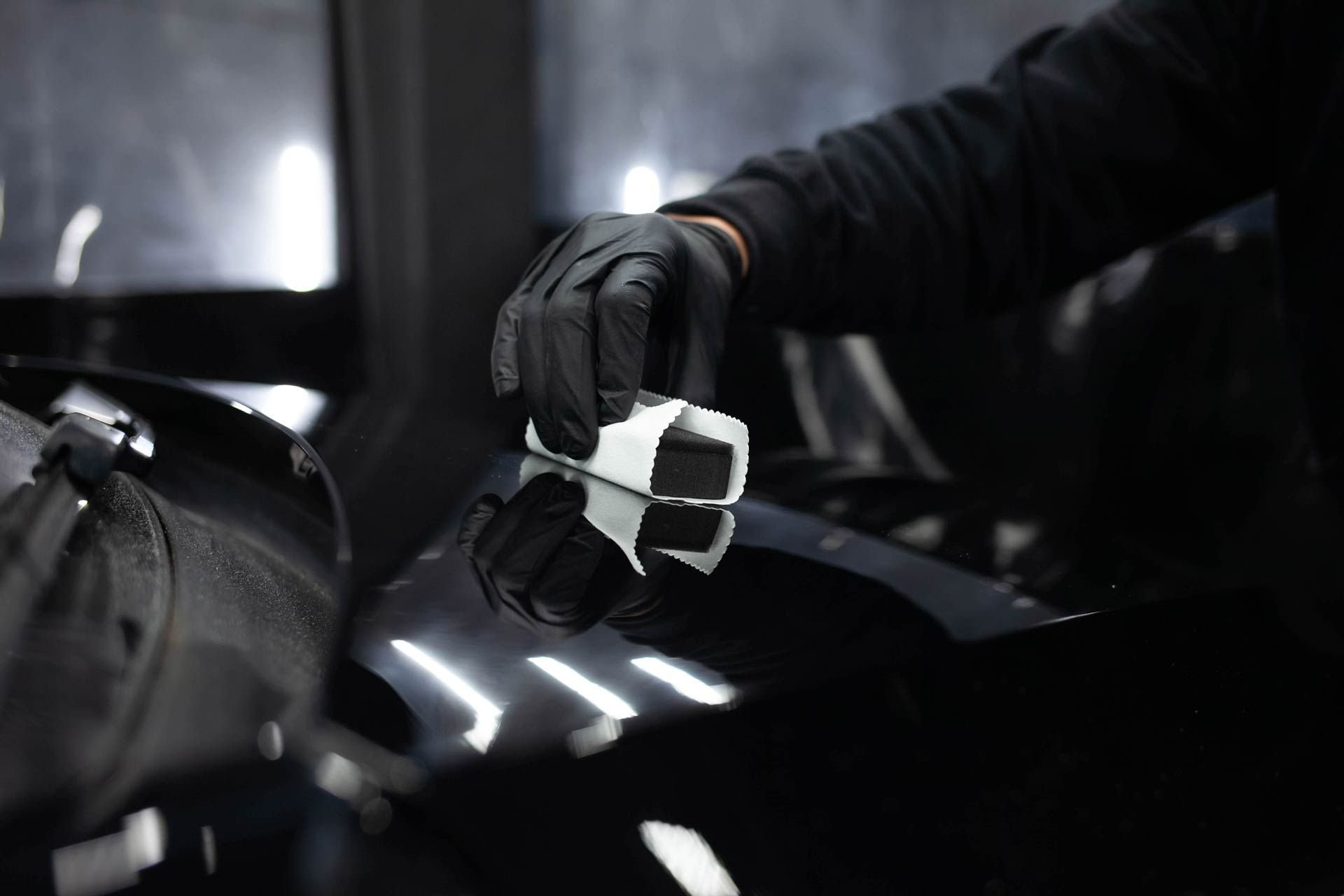
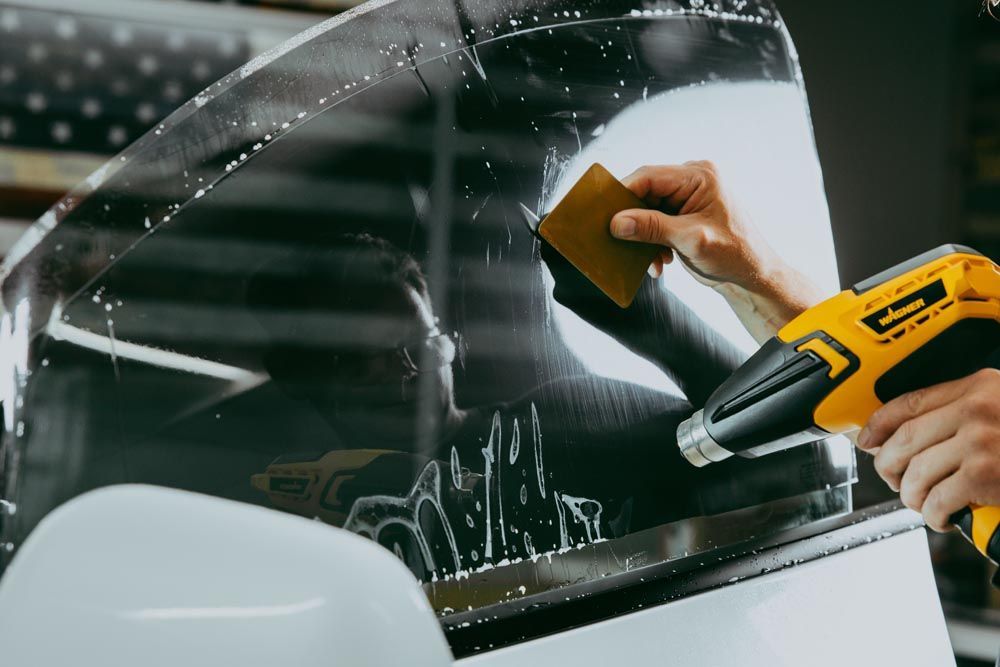